プラズマ窒化
プラズマ窒化とは
プラズマ窒化とは、グロー放電中においてプラズマ状態の窒素(N+)イオンと水素(H+)イオンをワーク表面に衝突させることによって行う窒化処理で、被加工物表面にFe窒化物が創生され、更に内側には窒素の拡散層が生成することにより、耐摩擦摩耗性のある表面処理が可能になります。(1961年まではイオン窒化とも言われていました)
以下に詳細な原理、原理図、応研のプラズマ窒化技術の特徴を述べます。
※JIS B 6915「鉄鋼の窒化及び軟窒化加工」に準拠
プラズマ窒化の原理
プラズマとは、固体、液体、気体に次ぐ第4の物質状態で、気体を構成する分子が電離し陽イオンと電子に分かれて運動している状態をいいます。
プラズマ窒化では、0.1~1kPa程度の「N2+H2」ガスで構成される希薄雰囲気の高真空炉体において、炉壁を陽極に、ワークを陰極にして数100V程度の直流電圧を印加すると、陰極直近で電圧降下(陰極降下)が生じ、その範囲内でグロー放電、すなわちプラズマ状態が発生して紫色に光ります。
このグロー放電中に存在する電離したN(+)とH(+)イオンは、陰極(ワーク)に向かって移動し、加速されて高速で衝突し、衝突時の高エネルギーは、熱エネルギーに変換されワークを加熱します。
この加熱と同時に、スパッタリング作用により、表面が清浄化され、さらにワークから叩き出されたFe原子とN原子が結合して表面にFe窒化物(プラズマ窒化では主にFe4N/γ’相、材質・条件によって一般的なFe2~3N/ε相)が創成され、さらに内側に窒素拡散層が生成します。
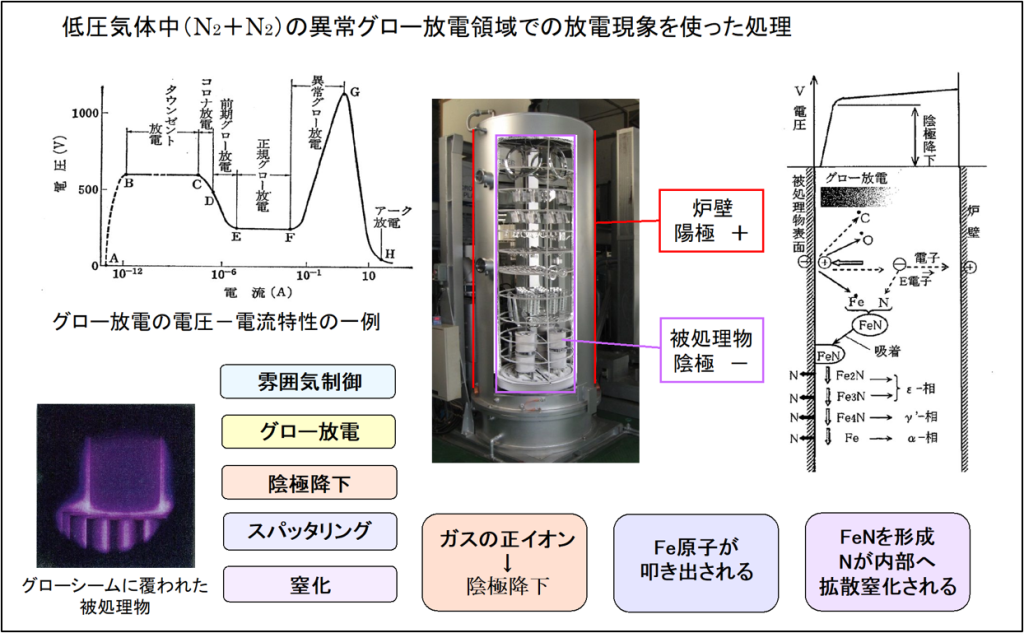
応研のプラズマ窒化技術
応研では、高周波熱処理と同様に、長年のプラズマ窒化に関する研究開発の成果、豊富な受託処理の経験を元に、独自のプラズマ窒化法の開発と改良を行い、複雑なお客様ニーズにもお応えしています。
主な技術ポイントは下記の通りです。
- 熱サイクル(加熱温度、炉内温度均一性、加熱時間、冷却方法)
- N2/H2ガス比率と導入タイミング
- ワークの炉内配置(窒化の均一性)
- 前洗浄方法
- 窒化防止策(ネジ穴、ネジ溝部など)
プラズマ窒化材の組織の特⾧
窒化された被処理物には、下図(左)に示すように、一般に、最表面から窒化化合物としてε相(Fe2-3N)、γ’相(Fe4N)が生成します(化合物層)。応研のプラズマ窒化処理は、独自のガス組成と処理温度の設定に加え、正確な温度制御とガス供給制御が特徴であり、ガス窒化処理と比較して、下図(右)のように、硬いが脆く剥がれやすい「化合物層」を薄くすることが出来ます。
プラズマ窒化処理 受託加工の事例紹介はこちら
高周波熱処理と同様に、プラズマ窒化処理でも上記の特徴を生かして、より高品質を得るために、お客様との情報交換、共有化を大事にしています。また、試作を含む小ロット処理にも応じますので、軸や歯車、しゅう動板、ガイドといった鉄鋼材料などの摩耗でお困りのかたは、ぜひ一度当研究所にご相談ください。
プラズマ窒化材の機械的性質・特性の特徴
- 耐摩擦摩耗性の向上
窒化化合物層(主にγ’相)が高硬さであることにより得られます。 - 低変形
プラズマ窒化では、一般的なガス窒化や塩浴軟窒化などと同様に450~550℃程度のAc1変態点以下の低温で数~数10時間、加熱処理され、焼入れを伴わない(変態変形が無く、炉冷ゆえ熱変形も少ない)ことにより得られます。 - ステンレス鋼(SUS304など)の窒化が可能
他のガス窒化などでは表面酸化膜の存在により処理は難しいですが、プラズマ窒化では表面酸化膜を(+)イオンでスパッタリングして除去するため処理可能です。
- 表面状態が良好(光輝性大、表面粗さ小)
(+)イオンによるスパッリング深さは浅いため、表面状態は処理前とほとんど変わらず綺麗で、表面状態の要求仕様・精度によっては後研磨工程の省略が可能になり、コストダウンが期待できます。 - 耐食性の向上
表面での窒化化合物の存在により、鋼種により耐食性の向上が図れます。 - 高温使用が可能
窒化一般に、500~550℃程度で処理されマルテンサイト変態を伴わないため、 Ac1変態点以下の高温で使用しても焼戻されず表面硬さの低下が無いため、高温環境での使用が可能です。(例:自動車エンジンのクランク軸)
主な参考文献(クリックして詳細を見る)
※入手ご希望の方は問い合わせフォームからお問い合わせください。
- 松岡裕明:応研所内資料(技術相談対応可能)
- 高瀬孝夫:「鋼の表面硬化法としての窒化」、鉄と鋼, 第66年、(1980) 第9号, P1423.
- 竹内博次:「プラズマを応用した表面改質技術」、熱処理、59、1、(2019)、p.4.
- 渡邊陽一:「窒化および軟窒化技術の現状と課題」、熱処理、61、3、(2021-6)、P.1.